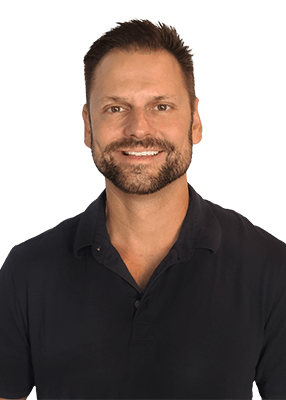
by Paul Wheaton
June 18, 2025
Construction takeoff is an essential piece of any construction project. Closely tied to estimating, takeoff looks specifically at measuring spaces and then calculating quantities of materials that are needed to ensure a project stays on time and on budget.
Whether you’re new to the construction industry or a seasoned professional, you might find yourself asking some questions about the takeoff process.
In this article, we’ve covered some of the most common takeoff questions to help you get the answers you need.
But takeoff is only part of the bidding process. So, if you have similar questions about construction estimating, check out the sister FAQ guide here.
What is Construction Takeoff?
Also known as quantity takeoff or material takeoff, construction takeoff is an itemized list of measurements of spaces and the physical materials needed for a project.
The term “takeoff” comes from the process of taking information from the project blueprints/models and using it to calculate area measurements and quantities of materials.
Unlike estimating, takeoff does not include calculating costs for things like labor, equipment, overhead and permitting.
Why is Construction Takeoff Important?
For a project to even get off the ground, every piece of material needs to be counted and calculated, and every space needs to be measured.
Takeoff is essential to ensure that you have all the materials and measurements you need for every stage of construction.
Imagine you are building a house and while framing, you discover that you are short on lumber. The result is a delay in production because you need to order more, and you now have an increase in cost from extra labor and materials.
And that is just one example of how takeoff affects construction projects.
Ultimately, the goal of takeoff is to measure spaces and count quantities of materials accurately as possible, so the bill of quantities can be used to determine a project’s costs, order materials and schedule construction.
But the benefits of takeoff extend far beyond just scoping a project’s area and calculating material needs. By leveraging quantity takeoff, you can:
- Enhance estimating accuracy
- Plan and manage projects more effectively
- Optimize project materials so there is no waste
- Manage change orders or avoid them altogether
- Mitigate risk with thorough documentation and record-keeping
- Gain an advantage in competitive bidding and contract negotiations
- Make informed financial decisions using accurate historical data
How is Takeoff Connected to Estimating?
You might be asking yourself, isn’t estimating and takeoff the same thing? Afterall, they both look at counting materials and use that to create budgets for a project.
So, what makes them different?
In simple terms, takeoff is mainly focused on quantifying and measuring materials and spaces, while estimating is focused on pricing those components, along with other costs, like labor, equipment and overhead. But they are indeed connected.
Think of takeoff as a slice of the larger estimating cake, playing a crucial role in the wider estimating process.
Takeoff provides the sturdy foundation that estimates can build upon, calculating measurements and quantities which will be evaluated, priced and compiled to give you a full detailed estimate of your project’s total costs.
Additionally, estimates and takeoffs have different uses.
For instance, contractors run takeoff for:
- Ordering materials
- Project planning
- Construction scheduling
While estimating focuses on:
- Identifying costs (materials, labor and overhead)
- Comparing vendor prices
- Bidding
- Contract negotiations
- Financial decision making
Accurate takeoff and estimating form the foundation of a successful project.
They need to work together, but this can sometimes be difficult without some helpful solutions at your disposal, like construction takeoff software.
How is Construction Takeoff Measured?
Most projects use a wide variety of materials, from roofing shingles to steel beams; all must be measured in the appropriate way.
Here’s the most common units of measurement for construction takeoff:
Length
- Inches (in) and feet (ft)
- Centimeters (cm) and meters (m)
- Used for linear measurements like pipes and electrical wiring.
Area
- Square inches (sq in) and square feet (sq ft)
- Square centimeters (sq cm) and square meters (sq m)
- Used for materials that cover surfaces, like flooring, siding and roofing.
Volume
- Cubic inches (cu in) and cubic feet (cu ft)
- Cubic centimeters (cu cm) and cubic meters (cu m)
- Used for materials that fill space, like concrete and blow-in insulation.
Weight
- Ounces (oz), pounds (Ibs)
- Grams (g) and kilograms (kg)
- Used for materials like steel and concrete.
Count
- Each (ea) and Unit (unit)
- Used for individual components, like windows, doors and fixtures.
Time
- Minutes (min) and hours (hr)
- Used for labor and equipment usage.
How is a Construction Takeoff Created?
The following outlines the general steps for the construction takeoff process, although this can vary depending on the size and type of the project.
- Gather and review the project documentation
-
- Take a thorough look at the blueprints and drawings to familiarize yourself with all the area specifications and material components, so you have a general idea of the scope of work.
- Break the project down into manageable pieces
-
- By dividing up the project and grouping elements, like the foundation, framing, plumbing, etc., you can more easily categorize and organize the material quantities later. However, this step doesn’t always apply for all specialized estimators. For example, an electrical estimators will instead divide the project by rooms and codes.
- In-depth analysis
-
- By taking a magnifying-glass approach to the blueprints, you can begin measuring spaces and itemizing every single piece of material. This is also when you might identify discrepancies or missing components on the drawings that you can flag back to the architect and client. By raising awareness of any issues early, you can avoid costly delays, prevent confusion and intercept potential client disputes.
- Take thorough measurements
-
- Using standardized units, measure the dimensions of every area (floors, walls, land) and material component. The type of object will determine how it gets measured, for example, lumber will be measured in length and concrete in volume.
- Count the quantities
-
- Using your measurements and the blueprints provided, calculate how much of each component you need. Total counts should be recorded in a spreadsheet or estimating software as part of the takeoff, but also to allow quick and simple viewing for estimators and other stakeholders.
- Factor in waste and allowances
-
- Buying exact amounts for items is a recipe for disaster. Think about how often materials like bricks or nails break while being handled or installed. By including additional quantities for high waste components, you can create a contingency cushion to prevent project delays.
- Review quantity calculations
-
- Double-check and validate that all your measurements and counts are accurate and cross-reference them with the project drawings. Once everything looks good, log the review so you have a reliable paper trail of documentation.
- Fill out a bill of quantities
-
- Finally, create a comprehensive bill of quantities that finalizes your calculations and will be used as the basis for cost estimating, ordering the materials and scheduling construction.
As you can see, the process of completing construction takeoff can be long and complex, especially when done manually. With the help of construction takeoff software, the whole process becomes much easier.
What are Some Common Challenges for Takeoff?
Construction takeoff is complex, and unfortunately, there are a lot of ways that it can get confusing, such as:
- Human error, using manual methods of calculating takeoff, especially if takeoff is not reviewed and verified by multiple estimators.
- Incomplete or unclear drawings provided by the owner and/or architect, which, if not caught, can lead to major takeoff errors and disputes.
- Forgetting to include phase-specific materials, like tarps, scaffolding and trench boxes.
The best way to handle these challenges is by approaching them head-on. Estimators and contractors who don’t anticipate mistakes won’t be prepared when they happen.
While communicating clearly with the client/architect and thoroughly reviewing measurements can help avoid these pitfalls, the best way to master takeoff is by utilizing takeoff software.
Advanced software features can give you the edge over the competition, making your takeoffs fast, accurate and profitable.
How Can Software Help With Takeoff?
If you’re using manual takeoff methods, you might not be able to keep up with today’s fast-paced and high-pressure construction industry.
Accuracy and speed are key to staying ahead of the competition, and construction takeoff software can help you achieve this.
With automated tools, you can utilize built-in formulas for accurate calculations, simplifying and speeding up the takeoff process.
You can also pull material and dimensional data from digital blueprints to quickly generate lists of material quantities and cross-check them with your measurements.
And with a robust software solution, you can unite both estimating and takeoff under a single all-in-one platform, eliminating costly data silos and streamlining your estimating.
What are the Benefits of Having an All-In-One Solution?
An all-in-one solution connects takeoff and estimating for faster, more accurate bidding.
By integrating estimating and takeoff under an all-in-one bidding platform, you can combine multiple tools into one comprehensive software package, all while keeping specific tasks distinct.
For example, you can design and build data on one screen for takeoff and seamlessly transfer that information over to another for estimating and pricing.
Automated data translation will eliminate wasteful double entry and the risk of input error and mistakes.
And from a financial standpoint, you can cut down on expenses from juggling maintenance and hardware costs between multiple systems.
With real-time data integration between estimating and takeoff, the whole process is streamlined, allowing you to create estimates within a fraction of the time.
Speed and accuracy are key to winning projects. The faster you submit an accurate bid, the more likely you will be to win the project, beating out the competition.
Ultimately, an all-in-one solution is built to ensure your projects will be fast, accurate and profitable in a way that no manual method ever could.
Effective Takeoff Using McCormick
The whole purpose of construction takeoff is to ensure a project has all the materials it needs to be completed on time and on budget. So, no matter what your trade, either plumbing, MEP or electrical, accuracy is critical at every stage, from reviewing the initial blueprints to measuring pipes, valves or electrical wire.
Construction takeoff software can help ensure precision and speed where manual takeoff methods cannot.
If you’re searching for a top-of-the-line solution, consider McCormick estimating and takeoff software with its industry leading service for the mechanical, electrical and plumbing trades.
McCormick not only helps you win more jobs, but also gives you access to advanced features that can:
- Cut down time spent on material calculations
- Seamlessly integrate takeoff and estimating
- Integration with other administrative systems, like accounting
- Reduce wasted materials
- Track and manage change orders
To learn more, contact one of our specialists today!
Share Article